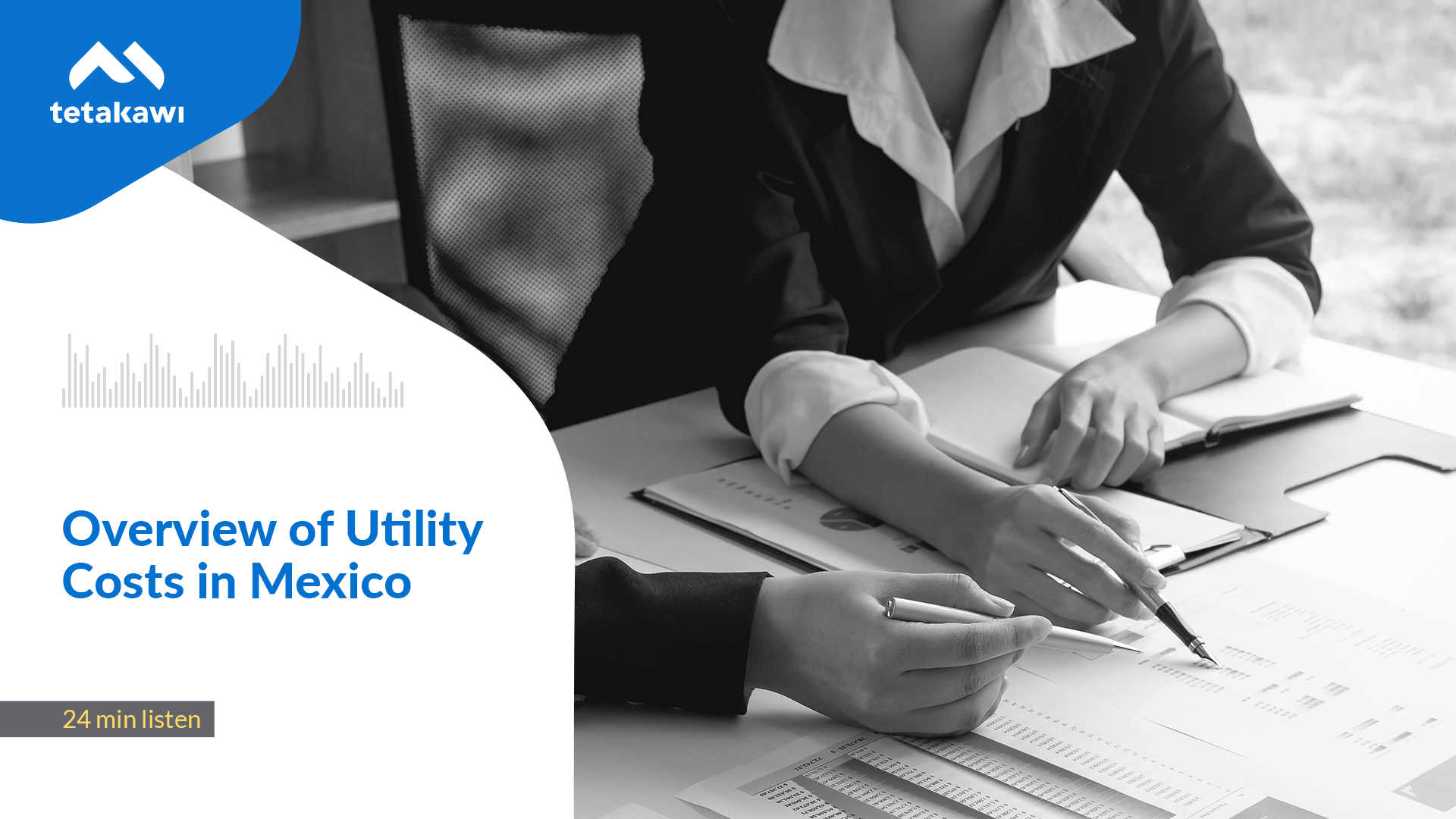
Show Notes:
Episode 6: Overview of Utility Costs in Mexico
In this episode, Ricardo Rascon and David McQueen build on their previous discussions about real estate and labor costs for manufacturers who expand to Mexico. In this conversation, Ricardo and David focus on other costs associated with manufacturing in Mexico: utilities, transportation, and more!
Starting with utilities costs, David clarifies that, for most companies, the utilities costs to be considered are electrical power, water, and possibly natural gas. Companies also need to plan for the costs of communications and services, which function a lot like utilities. Ricardo and David talk in the most depth about electrical service in Mexico, which is no different from that in the US in terms of voltage and frequency. The power quality is such that only the most sensitive applications will require power conditioning, up time is pretty good, outages are infrequent, and typical rates (through the main, state-run supplier, CFE) are comparable to or lower than rates in the US. To establish electrical power, a company must make sure to have adequate supply to its building, establish its peak demand, and evaluate transformer capacity. To connect machinery and equipment to its newly established power supply, the company will have to prepare a wiring plan for engineer approval before proceeding with connection to the power source. David explains the fees associated with the whole process of getting electrical power set up, including the bond CFE will ask for in order to get service started.
Moving forward, David addresses water, which is not very expensive in Mexico and follows similar discharge regulations as in the US, but can be a problem in terms of volume and availability and is generally not fit for drinking. Some companies may find themselves needing natural gas, and in this case they will have to deal with the distribution issues and possible connection fees, though cost is generally competitive. Regarding communications and systems, David notes that infrastructure in Mexico’s manufacturing regions is similar to that of the US. There is a whole range of available solutions, and some providers are the same as in the US.
Finally, David explains some other costs to consider before expanding into Mexico, such as employee transportation. Companies will also have to plan for the costs of goods and services, personal safety equipment, and the like, factoring in the relatively low cost of services and high cost of distribution. Startup costs must also be weighed, but that’s a topic for the next episode!
Thank you for joining us on Manufacturing in Mexico!
Links:
Visit our blog to learn more.
Episode Transcript
Speaker 1:
Welcome to Tetakawi's Manufacturing in Mexico Podcast, where we talk to internal and external experts to provide you with news, insights, and best practices about doing business in Mexico.
Whether you're thinking about expanding into Mexico or already there, this podcast will provide you with the information and advice you need to launch, operate, and thrive.
Ricardo Rascon:
Hello and welcome to another episode of the Tetakawi's Manufacturing in Mexico Podcast. My name is Ricardo Rascon, and today I'm joined again by David McQueen. Como estas, David?
David McQueen:
Glad to be back, Ricardo.
Ricardo Rascon:
That's great to hear. So on our last podcast, we talked about real estate costs in Mexico, and the one before that we discussed labor costs.
Now today we'll turn our attention to a few of the other costs that manufacturers could expect to incur when operating in Mexico. And more specifically, we're going to talk about utilities, transportation, and just overall general expenses.
So Dave, what do you have to tell us about utilities in Mexico?
David McQueen:
Well, Ricardo, I think for most companies the main things they need to consider with respect to utilities are electrical power, water, and possibly natural gas. We should probably also talk about communications and data services. These operate essentially like utilities.
Ricardo Rascon:
All right. So let's start dissecting these one by one. Let's talk about electricity first. What will I need to deal with in terms of different voltages or frequencies in Mexico?
David McQueen:
There's no difference to the United States. Electrical power in Mexico is available in the same nominal voltages and frequencies as the US. It is different from Europe and some other areas of the world, but single phase power is available in nominal voltages of 120 and 240, and 120 is the standard voltage for residential and light load use. Three phase power is available in 240 and 480, and the standard frequency in Mexico is 60 hertz.
Ricardo Rascon:
And what's the power quality like in Mexico, Dave?
David McQueen:
Well, it can run a bit hot and the frequency can be a bit low, but in general, only the most sensitive applications will need power conditioning. In most cases, conditioning is not required, and it's certainly not generally used.
Ricardo Rascon:
And what about uptime?
David McQueen:
It's pretty good by international standards. Outages are infrequent, and they're usually of short duration. Like most countries, weather's the most common cause of outages, but power's usually restored very quickly.
So unless you have a requirement for an uninterruptible power source, or you have some sensitive processes or equipment, it's very rare for companies to require generating capacity, or local power backup.
Ricardo Rascon:
Right. And who supplies electricity in Mexico? Is it private? Is it public?
David McQueen:
Electricity is supplied mainly by the state owned Comisión Federal de Electricidad, or CFE. The CFE controls most generation, most transmission, and most distribution.
Mexico was in the process of deregulating its electricity sector under the previous administration, but that process is essentially stopped, and some of the reforms have been reversed by the current administration. So the future of power and the electrical market isn't really clear yet.
Ricardo Rascon:
And what are the typical electricity rates that manufacturers should expect to see in Mexico?
David McQueen:
Well, for our client base, they currently run around 11 and a half cents US per kilowatt hour, and that includes demand charges, time of use, and power factor charges.
This is pretty competitive with most of North America for mid range industrial users, and it's lower than many US jurisdictions. It's also, incidentally, comparable to power rates. In China.
Mexico used to be a relatively high cost power jurisdiction with a lot of its power generated pretty inefficiently using fossil fuels. The deregulation era brought about a rate competition environment, and the investment was made in alternative power generation and efficiency improvements, renewable energy, that kind of thing.
But as I mentioned, changes by the current administration have reversed some of those trends. So the rates are certainly competitive right now, but it's not clear what the future might bring. So companies do need to consider that.
Ricardo Rascon:
And let's say I'm ready to get started in Mexico. What are the steps that I need to take to connect to electrical power?
David McQueen:
Well, first of all, you need to make sure there's adequate supply to the building you intend to occupy. We mentioned this in some of our previous podcasts on real estate, because you can find properties and buildings which are not adequately serviced, and then you might end up being responsible for the upgrade costs if so.
So you want it to be part of your negotiations. Same goes for connections. And in some cases power will be connected to your building by the landlord or the developer, but in other cases, you will have to do the connection yourself. You have to pay for it. Sometimes connecting to the mains is going to be your cost.
The next thing to do is establish your peak demand. CFE charges a one time fee of approximately $100 US per KVA for peak demand above 200 KVAs. Most industrial users will need more capacity than that, so you will need to pay the demand charge if you need more than 200 KVAs.
And just a warning, CFE monitors peak demand. If you exceed what you've paid for, they can and they do shut off the power supply.
Now, once you know your peak demand, then you'll need to look at transformer capacity. Landlords typically provide some level of transformer capacity with their buildings. They may even cover some of the demand charges if they provide more than 200 KVA. But usually they only include a minimal level of power which keeps the lights on. It maybe runs the office air conditioning, but it's not available for much else. So the tenant often has to provide whatever additional transforming capacities required, and as I mentioned, maybe pay that CFE demand charge.
Now when you're deciding on transformer capacity, CFE generally does not like people to exceed 80% of the rated capacity. So you're going to need to purchase a large enough transformer to make sure you don't exceed that limit.
And also, of course, it's usually more economical in the long run to install more transforming capacity than you actually require, to leave yourself some room for expansion. And incidentally, the available transformer capacity does not affect the demand charge you pay CFE. They're really only concerned about your actual peak demand is when they calculate and monitor your usage.
So you can always put in a larger transformer, but you only purchase the additional peak capacity when you actually need it.
Ricardo Rascon:
Perfect. So now I have power to my building, and I've installed a large enough transformer, and I paid for my peak demand. But what do I have to do to connect my machinery and equipment?
David McQueen:
Tenants and owners are typically going to be responsible for running the internal wiring in their buildings, as is the case in the United States. And the exception of that, of course, is whatever the landlord provides in terms of minimal lighting and office areas with perhaps outlets and air conditioning. Otherwise, you need to run the power yourself.
So to be permitted to run and connect the wiring, you will need to prepare a wiring plan that has to indicate the power loads you intend to connect, and the wiring that you plan to install in the circuits, and so on. This has to be reviewed by a Mexican electrical engineer who's going to certify it, and then submit it to CFE for their approval. And once CFE has approved it, then you can proceed with the work and connect to the power source.
There's a cost. Typically it's in the range of about $3,500 US for the process, including the engineering review. But more importantly, it takes time. So it's wise to start well ahead of when you want to occupy your building. I would recommend having a plan in place and approved at least three months ahead of when you plan to occupy your building. Longer if your wiring and connection work is extensive.
Ricardo Rascon:
Great. And anything else I need to take into account with respect to electricity?
David McQueen:
Yes. CFE is going to ask for a bond in order to start your service. The amount of the bond is based on your anticipated billings.
Now, most utilities and data providers are also going to ask for payment bonds. And in some cases you may be able to negotiate for the bond to be reduced or eliminated, but not with CFE. They're going to insist. Typically it's going to cost something like a $1000 to $5,000 US to put in place. Less if you use a small amount of power, more if you use more power.
Ricardo Rascon:
Great. So I think we now have a good understanding of how electricity works, how to get power connected, how to get our lights on, the estimated fees associated with payment bonds and expected demand.
So I think we're ready to move on to the other utility that you mentioned, which was water. What can you tell us about water in Mexico there?
David McQueen:
Well, first of all, water in Mexico is not very expensive. Typically runs around $0.70 US per gallon in most municipalities.
But there can be a problem with volume. Availability of water. There are some locations where water itself is actually restricted because of availability, but more often than not, it is a case of a distribution limitation. So you need to be aware of that.
Now, water use is often restricted for residential use. That's why you see those black tanks on top of houses in Mexico. They fill up during the nighttime hours when the water's available to the residences, and then they run the tank down during the day when it's not available.
Industrial users are not typically restricted respect to hours of use, but delivery capacity can still be an issue for high volume process water users. So just like electricity, if there isn't enough capacity or you're not connected to the mains, you can find yourself paying for those connections, or simply not having enough water available.
For example, in one of our west coast industrial parks, we actually built a desalination plant and a pumping station because the municipality simply could not deliver enough water through their mains to our clients.
Ricardo Rascon:
And throughout Mexico, will most of this water be potable?
David McQueen:
No, generally it will not be safe to consume. Surprisingly, municipal water is frequently treated and it's usually potable when it leaves the pumping stations. But the problem's in the distribution network. It usually doesn't have the integrity to maintain the purity.
So in most cases, people we will use tap water for everything but drinking. Bottled water's the most common solution for drinking water. But some companies install purification equipment and provide potable water in both offices and lunch areas. That solution is often used by restaurants and hotels. They install their own purification for drinking potable water.
Ricardo Rascon:
And are there any discharge regulations that we would have to keep in mind when operating in Mexico?
David McQueen:
Definitely. Water discharge regulations in Mexico are very similar to the United States. There are typically no additional charges for discharge. When you pay your water bill, it just includes your discharge charges. But you must complete an environmental survey and submit it for approval prior to beginning production. And one of the things that needs to be included in that is your water discharge treatment.
The treatment measures for any process water need to be identified along with any testing protocol that's required, and you can be charged and fined if you don't follow the protocol, or the treatment methods that were approved.
Ricardo Rascon:
So now we have water. We have power. What can you tell me about natural gas?
David McQueen:
Well, of course, building heat is not generally required in Mexico. So there are a few locations where freezing temperatures can occur with enough regularity that some electrical backup or emergency heating is included in the ventilation systems. But gas is not typically used for heating, and heat is often not provided at all, and not necessary.
However, natural gas is used extensively for industrial process locations in Mexico. The cost varies with the volume, but it's generally inexpensive and internationally competitive.
The problem, once again, can be distribution. There are many regions of Mexico that are well supplied with natural gas, but there are gaps. And even, in some cases, some industrial locations that do not have a supply. Industrial cities that don't have a supply of gas. And then within supplied regions, it's possible to find locations without gas service.
So once again, connection fees can apply, and you may be responsible for increasing supply to your building if it's not available. The main thing is to make sure it's available at your location if you require it for processing, and otherwise you can ignore the gas situation.
Ricardo Rascon:
So that seems pretty clear. So earlier you also mentioned communications systems. What is available to manufacturers in Mexico, and what are the typical costs for phone and internet service?
David McQueen:
Well, the communications infrastructure, at least in the industrial areas in Mexico, is very good and very similar to the United States. There are lots of providers who can provide landlines, data connections, cell phones, competitively with other regions of the world.
Cost of a landline is about $12 US per month, and a very basic internet connection can be as low as $25 US per month. Dedicated data connection lines are available anywhere between $450 and $18,000 US per month, depending on the speed you want and the volume of data you need, bandwidth you require. But the whole range of data solutions is available.
Cell phones, like in the US, are available in a wide range of plans. Very similar to the US, and the cost is comparable. There are several networks to choose from, including some that would be familiar as US providers.
Ricardo Rascon:
Right. So I think that covers utilities, but what other costs do companies need to consider before expanding into Mexico?
David McQueen:
Well, one you don't typically have in the US but you should think about in Mexico is employee transportation. The unskilled workforce are not usually going to own cars. If they do own cars, they won't be able to afford to drive them to work.
So when you consider the public transportation systems are often unreliable and inconvenient, companies frequently provide transportation for their employees. These are generally contracted out to various service providers. Those service providers can range from small vans to networks of very large buses depending on the volume and needs of the employer.
Employers are usually going to establish pickup zones around clusters of employees rather than door to door service. But some companies use door to door service as a perk for valuable skilled employees. So the option's there.
Salaried employees and many tradespeople are going to have their own vehicles and then drive themselves to work. So transports not typically of interest to them.
Ricardo Rascon:
So from an employer perspective, Dave, this sounds pretty complicated and expensive. Is this something that you really need to do, and what is it going to cost?
David McQueen:
Well, yeah, there is some work to scheduling and planning a cost effective transportation system for sure. But our studies have shown that transportation is not only the most important benefit to unskilled employees, but it's one they will change employers for, just to improve it. So yes, if at all possible you should transport your workers to your place of employment.
The cost varies depending on your location. If you're located outside of municipality and you aren't really close to where your employees live, you might spend upwards of $150 US per month per employee to get them to work. But if your employees live nearby and you concentrate recruiting on clustering your employees, then you might be as low as $30 per month per employee.
Of course, volume's also a factor. A small employer can expect to pay a lot more for a less efficient system using smaller vehicles, more pickup points, whereas a large employer can load up full size buses and lower their unit cost.
Another way to lower your cost is to locate in a park where a shared transportation system is provided to all the tenants of that park. And then there's a much larger critical mass, and so the unit costs are lower. Also, typically, the provider of that park will organize the transportation network. So you don't have the complexity of determining routes and pickup points and so on. They're going to do that for you.
Some shelter companies, Tetakawi among them, offer this type of service in their industrial parks, as do a few non-shelter parks. So that's another option.
Ricardo Rascon:
Great. So now I have power, I have water, I have gas. The phones are ringing, the internet works, and we have a way to get people to work. But what other cost factors do we need to consider?
David McQueen:
Well, everybody needs a basket of goods and services, of course. Everything from spare parts to personal safety equipment, stationary. Services like forecourt maintenance, careers, waste management.
Now of course, the actual list is going to vary considerably from one company to another, or from one industry to another. But in order to estimate your operating costs in Mexico, these expenses need to be considered in some detail in fact.
For me, when I was planning my operation from Mexico, one of the hardest budgeting challenges was assembling the list of indirect purchases, and understanding what drove those costs and what they were going to be in my operation in Mexico.
Most companies, these items are generally under a bunch of GL codes. A lot of them tend to be either small or on their own. They're relatively stable. So you don't pay too much attention to them. They don't get a lot of analysis. Not like labor or something else that's front of mind. But when you launch a new operation in a new country, there can be surprises. So you really do need to dig into this number and understand it.
Ricardo Rascon:
Perfect. So building off of that word surprises, what should we be looking out for in Mexico?
David McQueen:
Well, generally speaking, distribution costs in Mexico are higher than in the United States. So often the very same item will cost more to purchase in Mexico than it does in the US. Even if it's made in Mexico, it might cost more.
So depending on the volume, in Mexico it can be a little bit more, or it could be a lot more.
Conversely, because of lower wages, services are generally much less expensive in Mexico. So when you move your indirect purchasing to Mexico and start buying things there, you can expect to see increases in your purchase goods costs and reductions in your service costs. Depending on what you buy and the mix, your costs can either increase or decrease, and sometimes it can be significant.
Ricardo Rascon:
Interesting. And what can companies do to estimate and control these costs?
David McQueen:
Well, I would suggest that the first thing to do is to examine your current indirect purchasing, wherever you're located, very carefully. You not only need to know what you buy, but what drives that volume? Is it a per head expanse? Is it driven by production volume? Is it per square foot, or is it some other thing?
Once you know what need and what drives your volumes, then you can factor it for your Mexican operation, whatever size it's going to be, and however big an operation is going to be. You will of course need to increase travel and training budgets. Those will be higher than normal, but otherwise the same drivers generally apply.
So that's how I did it. This is probably what works best.
Another thing to do is to look at any large volume or specialized goods or services that you purchase. Now, certain expendable tooling, for example, that can be an item that is considerably more expensive to purchase in Mexico. On the other hand, vehicle maintenance is generally much less expensive.
Now, if your list is roughly balanced between goods and services, and there are no really specialized or large volume items, you're probably safe to conclude that the same net costs you currently incur in the US are close to what you're going to expect in Mexico, if you adjust it for the difference in volumes on the various drivers.
However, if there's an imbalance or some large volume or some specialized items, it's definitely worth checking the prices and determining what it's going to cost you in Mexico.
Now, if you run up against items which are more costly to buy locally than you can spend in the US, you can consider importing them from the US. Most companies are going to be Emex registered exporters, and that'll let you import from the US with no tax or tariffs. So you have that option. You can import the item that you need in Mexico from the US and use it in Mexico.
On the other hand, purchasing as many services as possible in Mexico, including perhaps some of those that your US location requires, that's going to lower costs. So you can look at changing where you purchase for both of your locations to optimize that situation.
Ricardo Rascon:
Sounds pretty complicated, Dave.
David McQueen:
Well, it takes a bit of effort, but indirect purchases collectively are often a very significant cost factor when you bundle them all together. So a bit of diligence can help to avoid a nasty surprise, and it can also make sure you don't miss that potential savings that could be significant.
Ricardo Rascon:
And Dave, have you ever seen these indirect purchases throw off a company's plan for expanding it into Mexico, and maybe they say, "Oh man, this is more expensive than I thought it would be"?
David McQueen:
Yeah, we have seen it happen. Usually it's related to some specialized item that, for whatever reason, is more significantly expensive in Mexico than it is in the US.
In the case of purchases, since the importation option is there, unless the item is large... I remember once there was a company with a lubricant that was very specialized, and they did have the option of purchasing it from the US, but the cost of transportation was significant, so they still ended up with a sizeable cost increase.
So yes, it can happen. The flip side can happen as well. We know of many companies in our client base who have identified service operations that are done for their US or other global locations that can be done in Mexico more cost effectively, and that they therefore move to Mexico and have them done in Mexico. So we've seen both happen.
Ricardo Rascon:
Great. Perfect. And thanks again for your time, Dave, and your insight. I think we've really delved deep into utilities, transportation, and some other costs here.
And I think over the last three podcasts, we've done a good job just helping companies understand, from an operational perspective, what it takes to operate in Mexico.
Now on our next podcast, we'll address the one time startup costs that these companies should also expect. So please join Dave and I as we discuss this very important and often overlooked topic.
Thank you again everyone for listening.
Speaker 1:
We appreciate you joining us for this session of the Manufacturing in Mexico Podcast. For more information and resources about how to succeed in Mexico, be sure to visit our website, tetakawi.com.